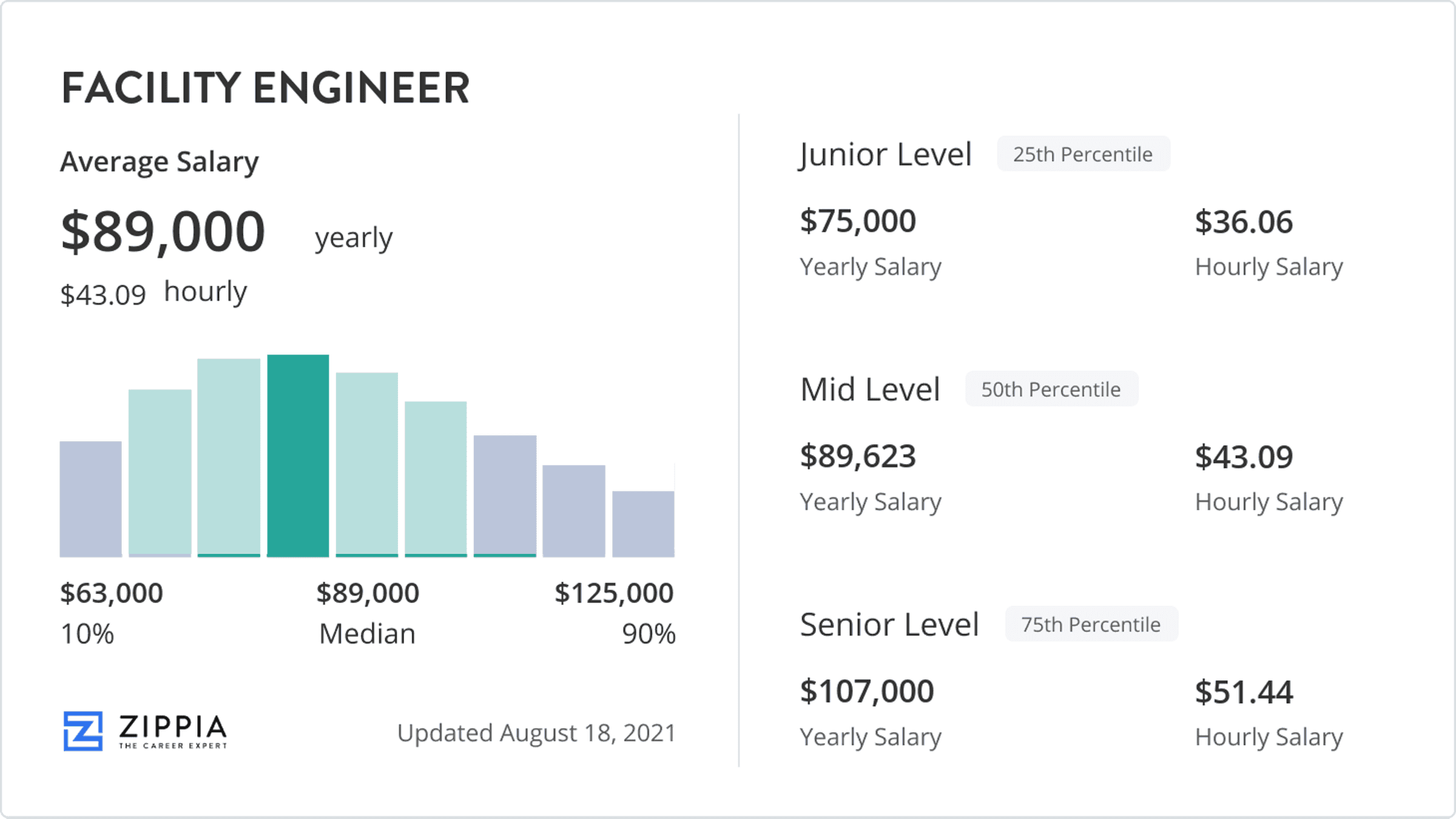
While value stream mapping is a way to improve your manufacturing process, it's not always easy. It involves mapping product family and products. You will need to train your team and possibly have a value stream supervisor. Your team should get support from the leadership in order to successfully implement the strategy. Larger companies will often have their own value streams managers who manage the mapping process. Even though smaller companies can manage without a VSM Manager, it is a good idea to let the leadership know the possible improvements.
Lean Six Sigma
Value Stream Mapping is a method that allows you to track the flow of information between customers and suppliers. The first thing to put on your value stream map is your customer. Start with the shipping area and work your ways upstream. Include a box that contains customer's data. This will show you how often the product must be made to meet the demand. Also, you will need to know the Takt (the time it takes to make a product) and how it compares with the product's cycle time. If Takt time is greater than the cycle, it could indicate a bottleneck.
Value stream maps can be used to help companies identify and eliminate waste in every stage of their business processes. Value stream mapping helps you to identify and analyze non-value-added activity and the flow information. It's also a useful tool to identify bottlenecks, and where improvements can be made in order to make the process more efficient. Value Stream Mapping can have many benefits, beyond just improving information flow. Value Stream Maps can be a valuable tool that will help you implement Lean Six Sigma.
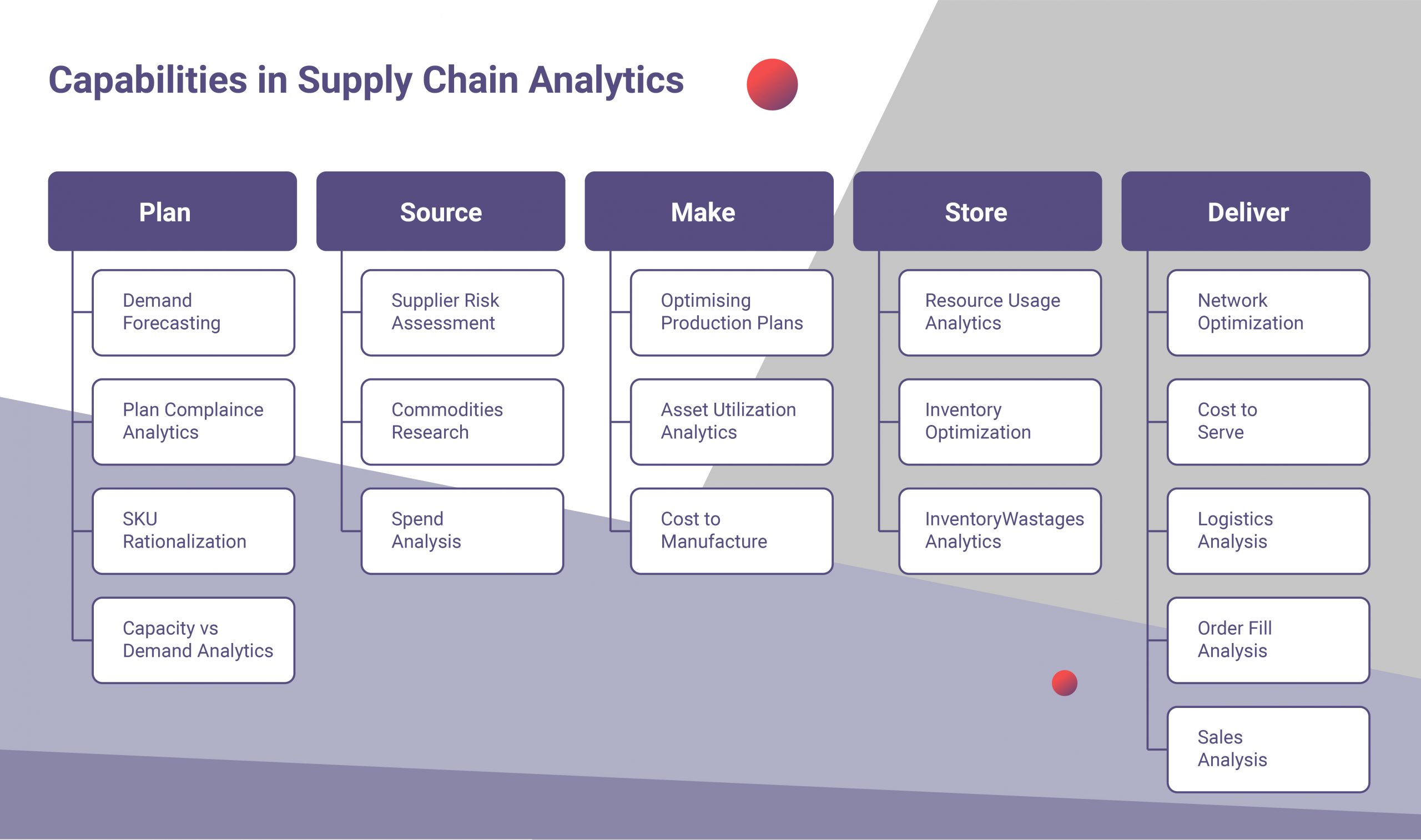
Lean Healthcare
Value stream mapping is a tool that helps improve the coordination of activities in medical fields. It helps identify areas that need improvement and recommends ways to implement them. A map might show a patient’s flow from the time they arrive at the hospital up to the time they leave after their treatment. By visualizing these flow paths, you can create a timeline for the whole process and identify value-added activities and waste-generating steps.
In order to make VSM in Lean Healthcare more effective, the authors recommend setting up clear definitions of the terms used in the process. The authors recommend that you establish appropriate indicators and share examples of success and failure. These will allow the results to be replicated and modified for specific situations. Lean approaches in the healthcare industry are more likely for positive outcomes. The authors suggest that there be a common definition and use of value stream mapping within the healthcare sector to ensure that these benefits are shared across the entire health care system.
Lean Manufacturing
To begin implementing value stream mapping, it is important to gather input from key stakeholders within a process. This team should include the people responsible for fulfilling customer needs. They should also include people who perform critical tasks and activities to ensure the flow of information. By gathering input from these key stakeholders, value stream mapping can help identify waste, and ultimately improve efficiency. The scope of the value streaming mapping process must be defined.
Next, you will need to choose the product/process that needs improvement and then train the team in value stream modeling. The mapping process begins with customer needs. It includes everything from when the customer is contacted to the decision making and communication that follows. Value stream mapping seeks to eliminate waste, make the process more efficient, and improve customer satisfaction. Lean manufacturing can provide a viable, sustainable solution that addresses the unique challenges faced by any company by identifying and eliminating those elements.
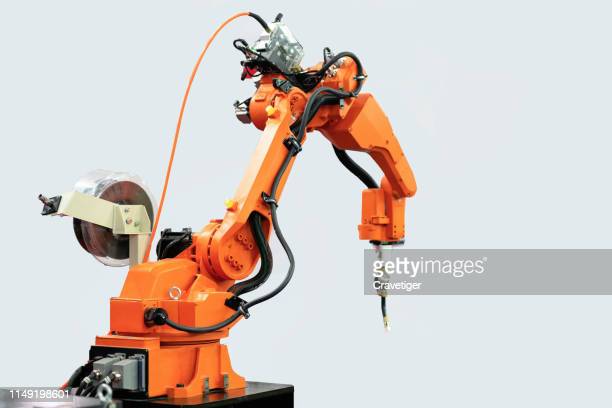
Future state value stream mapping
Future state value streaming mapping is an excellent tool to identify waste. This type of mapping helps to identify the causes and eliminate them. Future state ideas can be marked with the exact same symbols as current state maps. Takt Time is an important concept to consider in future state value stream mapping. It allows you to efficiently allocate resources and to identify waste areas. The future state-value stream map can also be a powerful tool in your company's arsenal.
Once you've determined where problems are and how they relate to the future state, it's time to map the steps you need to take to get there. Teams can use a future map as a reference tool to help them complete their projects and achieve the target values. It's essential to update your future state value stream mapping every six to twelve months, so you can measure your progress as it occurs. The future state map must be updated with new projects implemented or changes made.
FAQ
What is production planning?
Production Planning involves developing a plan for all aspects of the production, including scheduling, budgeting, casting, crew, location, equipment, props, etc. This document ensures that everything is prepared and available when you are ready for shooting. You should also have information to ensure the best possible results on set. This includes information on shooting times, locations, cast lists and crew details.
The first step in filming is to define what you want. You may have decided where to shoot or even specific locations you want to use. Once you have identified the scenes and locations, you can start to determine which elements are required for each scene. If you decide you need a car and don't know what model to choose, this could be an example. If this is the case, you might start searching online for car models and then narrow your options by selecting from different makes.
After you have chosen the right car, you will be able to begin thinking about accessories. What about additional seating? Or perhaps you need someone walking around the back of the car? Maybe you'd like to change the interior from black to a white color. These questions will help guide you in determining the ideal look and feel for your car. The type of shots that you are looking for is another thing to consider. Do you want to film close-ups, or wider angles? Perhaps you want to show the engine or the steering wheel? This will allow you to determine the type of car you want.
Once you've determined the above, it is time to start creating a calendar. You can use a schedule to determine when and where you need it to be shot. You will need to know when you have to be there, what time you have to leave and when your return home. Everyone will know what they need and when. You can also make sure to book extra staff in advance if you have to hire them. You should not hire anyone who doesn't show up because of your inaction.
You will need to factor in the days that you have to film when creating your schedule. Some projects only take one or two days, while others may last weeks. It is important to consider whether you require more than one photo per day when you create your schedule. Multiple takes of the same location will lead to higher costs and take more time. It's better to be safe than sorry and shoot less takes if you're not certain whether you need more takes.
Budget setting is an important part of production planning. You will be able to manage your resources if you have a realistic budget. Keep in mind that you can always reduce your budget if you face unexpected difficulties. However, it is important not to overestimate the amount that you will spend. If you underestimate how much something costs, you'll have less money to pay for other items.
Planning production is a tedious process. Once you have a good understanding of how everything works together, planning future projects becomes easy.
What is the role of a production manager?
A production planner makes sure all project elements are delivered on schedule, within budget, as well as within the agreed scope. They make sure that the product and services meet client expectations.
What types of jobs can you find in logistics
There are many kinds of jobs available within logistics. Here are some examples:
-
Warehouse workers - They load trucks and pallets.
-
Transport drivers - These are people who drive trucks and trailers to transport goods or perform pick-ups.
-
Freight handlers – They sort and package freight at warehouses.
-
Inventory managers – These people oversee inventory at warehouses.
-
Sales reps are people who sell products to customers.
-
Logistics coordinators: They plan and manage logistics operations.
-
Purchasing agents are those who purchase goods and services for the company.
-
Customer service representatives are available to answer customer calls and emails.
-
Shippers clerks - They process shipping order and issue bills.
-
Order fillers – They fill orders based upon what was ordered and shipped.
-
Quality control inspectors are responsible for inspecting incoming and outgoing products looking for defects.
-
Others – There are many other types available in logistics. They include transport supervisors, cargo specialists and others.
How can we increase manufacturing efficiency?
First, determine which factors have the greatest impact on production time. We then need to figure out how to improve these variables. If you don’t know where to begin, consider which factors have the largest impact on production times. Once you identify them, look for solutions.
Statistics
- (2:04) MTO is a production technique wherein products are customized according to customer specifications, and production only starts after an order is received. (oracle.com)
- [54][55] These are the top 50 countries by the total value of manufacturing output in US dollars for its noted year according to World Bank.[56] (en.wikipedia.org)
- Many factories witnessed a 30% increase in output due to the shift to electric motors. (en.wikipedia.org)
- Job #1 is delivering the ordered product according to specifications: color, size, brand, and quantity. (netsuite.com)
- It's estimated that 10.8% of the U.S. GDP in 2020 was contributed to manufacturing. (investopedia.com)
External Links
How To
How to Use the 5S to Increase Productivity In Manufacturing
5S stands to stand for "Sort", “Set In Order", “Standardize", and "Store". The 5S methodology was developed at Toyota Motor Corporation in 1954. It helps companies achieve higher levels of efficiency by improving their work environment.
This method aims to standardize production processes so that they are repeatable, measurable and predictable. This means that every day tasks such cleaning, sorting/storing, packing, and labeling can be performed. Through these actions, workers can perform their jobs more efficiently because they know what to expect from them.
Implementing 5S involves five steps: Sort, Set in Order, Standardize Separate, Store, and Each step requires a different action, which increases efficiency. You can make it easy for people to find things later by sorting them. When items are ordered, they are put together. Next, organize your inventory into categories and store them in containers that are easily accessible. Labeling your containers will ensure that everything is correctly labeled.
Employees must be able to critically examine their work practices. Employees need to be able understand their motivations and discover alternative ways to do them. In order to use the 5S system effectively, they must be able to learn new skills.
The 5S Method not only improves efficiency, but it also helps employees to be more productive and happier. They feel more motivated to work towards achieving greater efficiency as they see the results.