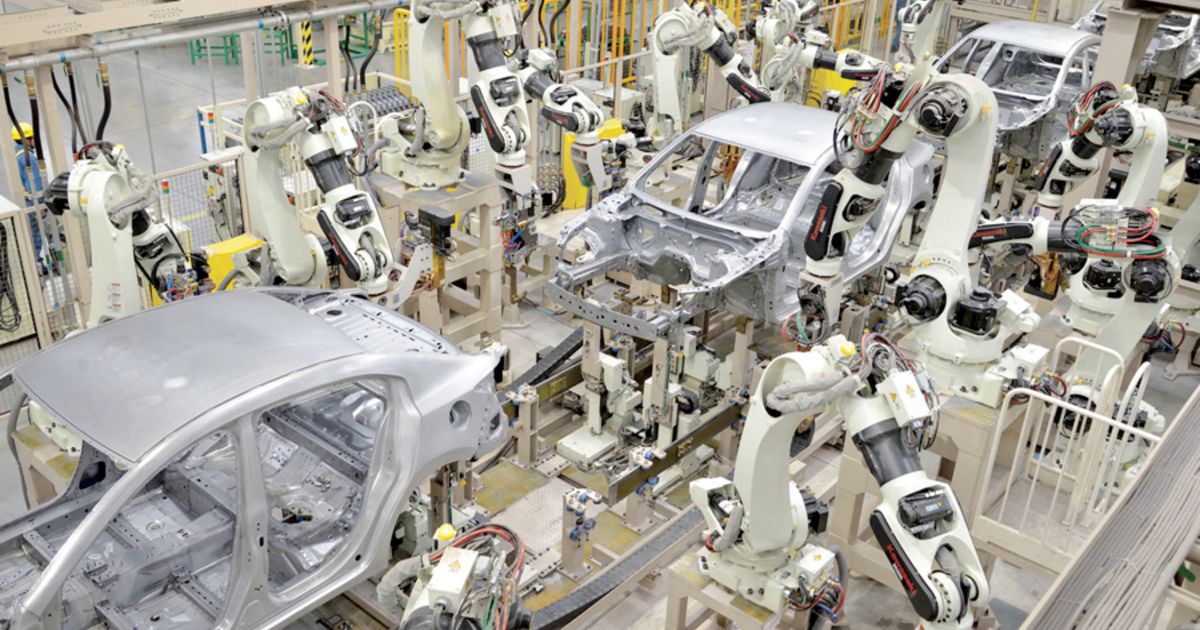
But value stream mapping can make your manufacturing processes more efficient. It's not simple. It involves mapping product families and products. Training is essential for the team. You might also need a value-stream manager. The leadership should also be involved in the implementation of the strategy. Larger companies may have their own value stream managers to oversee the mapping process. Although smaller companies may be able to do without a VSM manager it is beneficial to communicate with the leadership about the potential improvements.
Lean Six Sigma
Value Stream Mapping with Lean Six Sigma allows you record the flow from customers to suppliers using Value Stream Mapping. Your customer is the first thing you should put on your value streammap. Start at the shipping point and work your way upstream. Include a box that contains customer's data. This will show you how often the product must be made to meet the demand. You'll also need to know the Takt time (the amount of time it takes to produce a product), and how it compares to the cycle time of the product. If Takt time is greater than the cycle, it could indicate a bottleneck.
Value Stream Maps help companies identify waste at all stages of their operations. Value stream mapping helps you to identify and analyze non-value-added activity and the flow information. It can help you identify bottlenecks in your business and pinpoint areas where you can make improvements to make it more efficient. Value Stream Mapping is a great tool for improving information flow. It can help you implement Lean Six Sigma and increase your bottom line.
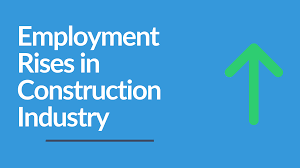
Lean Healthcare
Value stream mapping is a tool that helps improve the coordination of activities in medical fields. It helps to identify areas of improvement and provides strategies for implementation. A map, for example, can show how a patient flows from the moment they arrive at the hospital to the time when they leave the hospital after treatment. These flow paths can be visualized to create a timeline and identify waste-generating and value-added steps.
To make VSM in Lean Healthcare more efficient, the authors recommend that clear definitions be established for all terms. The authors recommend that you establish appropriate indicators and share examples of success and failure. This way, the results can be replicated and adapted to fit specific situations. Lean approaches in the healthcare industry are more likely for positive outcomes. The authors recommend that healthcare professionals agree on a common definition for value stream mapping to ensure that this methodology is widely used.
Lean Manufacturing
Before you begin to implement value stream mapping, gather input from key stakeholders. This group should include those responsible for meeting customer needs. They should also include people who perform critical tasks and activities to ensure the flow of information. By gathering input from these key stakeholders, value stream mapping can help identify waste, and ultimately improve efficiency. To begin, define the scope of the value stream mapping process.
Next, select the product or process to improve and train the team on value stream mapping. The mapping process starts with the customer's needs and covers all aspects of the decision-making, communication and communications processes. Ultimately, value stream mapping aims to eliminate waste and make the process more efficient, while improving customer satisfaction. By identifying the elements that contribute to customer satisfaction and removing them, lean manufacturing can become a viable, sustainable solution for the challenges facing any company.

Future state value stream mapping
Future state value stream mapping, if you've never heard of it before, is an excellent tool for identifying and eliminating waste. This type is used to find the causes of and eliminate waste. Future state ideas are marked with the same symbols as current state mapping. Takt Time is important to be aware of when planning for future state value streams mapping. It allows you to efficiently allocate resources and to identify waste areas. A future state value stream chart can be an effective tool for your company.
Once you have determined the root causes of the problems, and the relationship with the future state, you can map the steps required to get there. As teams complete projects and achieve the target value, a future state map can serve as a constant reference point. You need to keep your future state value stream map updated every six to 12 months so that you can track your progress. The future state map must be updated with new projects implemented or changes made.
FAQ
What does it mean to warehouse?
A warehouse, or storage facility, is where goods are stored prior to being sold. It can be an indoor space or an outdoor area. It could be one or both.
What is the difference between Production Planning, Scheduling and Production Planning?
Production Planning (PP) refers to the process of determining how much production is needed at any given moment. This can be done by forecasting demand and identifying production capabilities.
Scheduling involves the assignment of dates and times to tasks in order to complete them within the timeframe.
How can manufacturing efficiency improved?
First, identify the factors that affect production time. The next step is to identify the most important factors that affect production time. If you don’t know how to start, look at which factors have the greatest impact upon production time. Once you identify them, look for solutions.
Is automation important in manufacturing?
Automation is important not only for manufacturers but also for service providers. It enables them to provide services faster and more efficiently. It reduces human errors and improves productivity, which in turn helps them lower their costs.
Statistics
- According to the United Nations Industrial Development Organization (UNIDO), China is the top manufacturer worldwide by 2019 output, producing 28.7% of the total global manufacturing output, followed by the United States, Japan, Germany, and India.[52][53] (en.wikipedia.org)
- [54][55] These are the top 50 countries by the total value of manufacturing output in US dollars for its noted year according to World Bank.[56] (en.wikipedia.org)
- In 2021, an estimated 12.1 million Americans work in the manufacturing sector.6 (investopedia.com)
- You can multiply the result by 100 to get the total percent of monthly overhead. (investopedia.com)
- Many factories witnessed a 30% increase in output due to the shift to electric motors. (en.wikipedia.org)
External Links
How To
How to use 5S in Manufacturing to Increase Productivity
5S stands to stand for "Sort", “Set In Order", “Standardize", and "Store". Toyota Motor Corporation created the 5S methodology in 1954. It assists companies in improving their work environments and achieving higher efficiency.
The idea behind standardizing production processes is to make them repeatable and measurable. Cleaning, sorting and packing are all done daily. Because workers know what they can expect, this helps them perform their jobs more efficiently.
There are five steps that you need to follow in order to implement 5S. Each step requires a different action to increase efficiency. By sorting, for example, you make it easy to find the items later. When you arrange items, you place them together. You then organize your inventory in groups. Finally, when you label your containers, you ensure everything is labeled correctly.
This requires employees to critically evaluate how they work. Employees should understand why they do the tasks they do, and then decide if there are better ways to accomplish them. They will need to develop new skills and techniques in order for the 5S system to be implemented.
The 5S method increases efficiency and morale among employees. Once they start to notice improvements, they are motivated to keep working towards their goal of increasing efficiency.