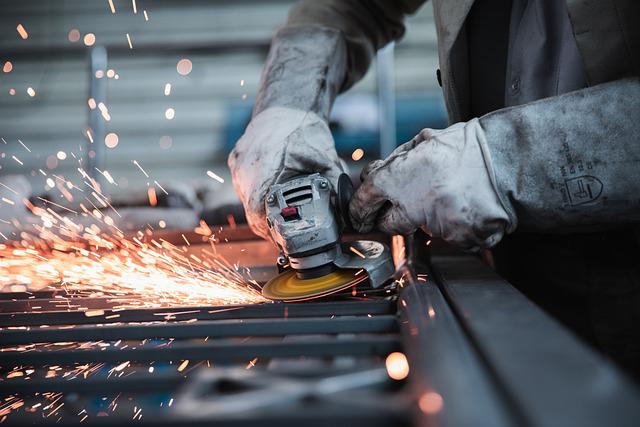
Manufacturing Extension Partnerships (MEP) Centres offer a variety of services for small and medium sized manufacturers. MEP Centers can be found in all 50 states and Puerto Rico. They are trusted advisors who help manufacturers identify growth opportunities and solve their challenges.
MEP Centers hire subject matter professionals who have knowledge of the local industry as well as experience in helping small and middle-sized manufacturers. The centers can assist in several areas including cybersecurity protection, productivity, quality and business growth. Sharon Ohman of Purdue University’s MEP center, Fort Wayne, said that SMMs could also use the tools they create internally or in collaboration with their suppliers.
The federal government pays half of the funding to each center. The rest is paid by local and state governments, or by private organizations. The American Innovation and Competitiveness Act, which was passed in January 2017, adjusted the cost-share ratio for MEP Centers. This allowed them to keep more of their nonfederal funds.
Some MEP centers are run by non-profit organizations, while others are affiliated with universities. Other MEP centers are operated by the state government or an agency within the same state as the center.
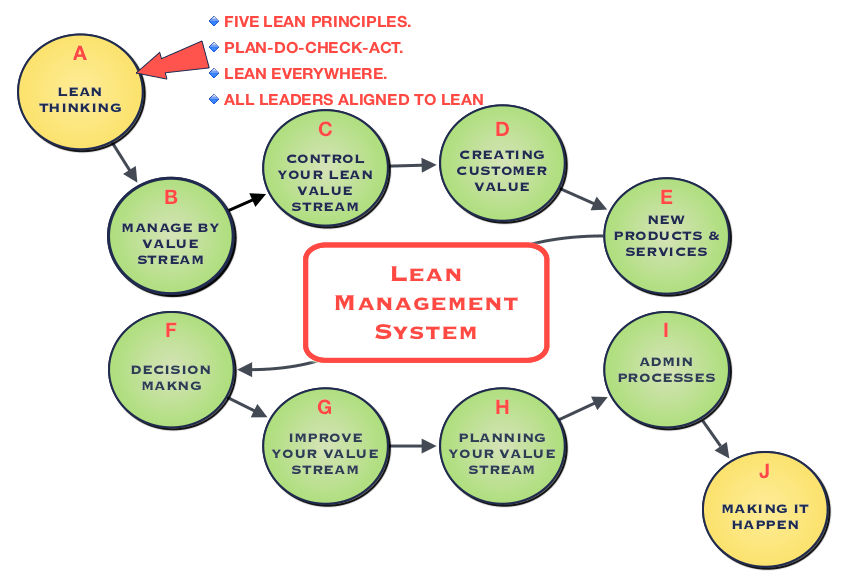
These centers could be staffed either by professionals, managers or consultants. Some centers are equipped with laboratories and research centers.
Some centers offer consulting and training services to other businesses. Nebraska MEP offers support to manufacturers in implementing new technologies.
MEP Services can be offered to a manufacturer’s employees or the company. Some centers have experts who travel to the manufacturing site to work together with a manufacturer’s leadership team to achieve specific goals.
MEP Centers have been in contact with more than 3,500 manufacturers over the past year. That helped them generate $14.4 billion in sales, $1.5 billion in cost savings, $5.2 billion in new client investments and helped create and retain 125,746 jobs across the U.S.
The MEP National Network includes 51 MEP Centers (including the NIST MEP Office) and an MEP Board. These partners can play an important part in the success the MEP system. They will help ensure that it is effective and has the capability to expand to U.S. manufacturer in the near future.
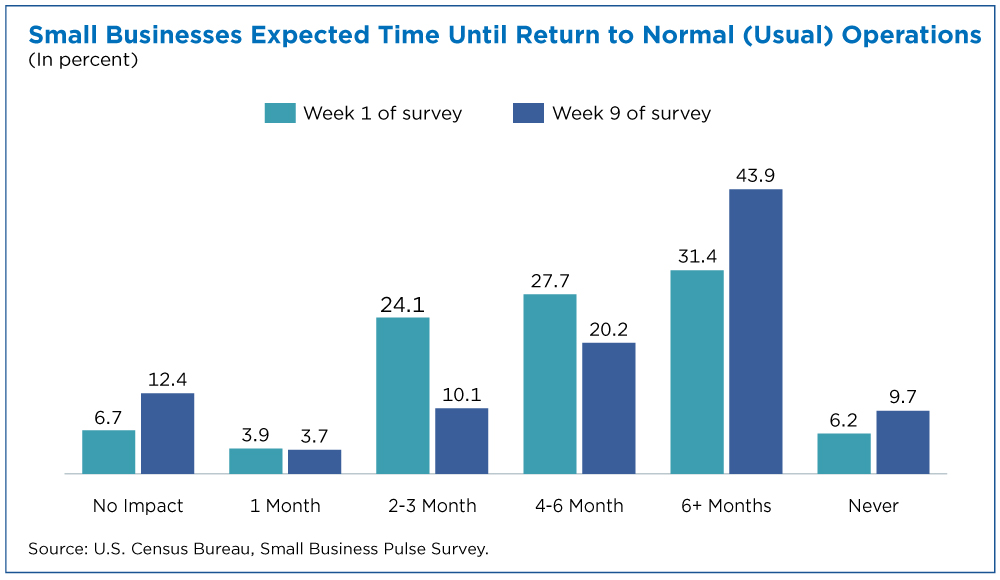
Through its information infrastructure services and pilots, the MEP Network is assisting MEP centers and smaller manufacturers in accessing the technical information they need to operate their businesses. These projects will accelerate the adoption and use of electronic commerce among MEP centers, smaller manufacturers and other businesses.
In addition, the MEP National Network is a key component of a larger national strategy to increase the capacity of small and medium-sized manufacturers to adopt technology to support their business and economic growth. The MEP National Network is in contact with over 7,000 American manufacturers a day. This network's work increases innovation, job growth, and economic growth.
FAQ
What are the 7 Rs of logistics management?
The acronym "7R's" of Logistics stands for seven principles that underpin logistics management. It was created by the International Association of Business Logisticians and published in 2004 under its "Seven Principles of Logistics Management".
The acronym is composed of the following letters.
-
Responsible - ensure that actions are in compliance with legal requirements and do not cause harm to others.
-
Reliable - Have confidence in your ability to fulfill all of your commitments.
-
Be responsible - Use resources efficiently and avoid wasting them.
-
Realistic – Consider all aspects, including cost-effectiveness as well as environmental impact.
-
Respectful: Treat others with fairness and equity
-
Resourceful - look for opportunities to save money and increase productivity.
-
Recognizable is a company that provides customers with value-added solutions.
What is the importance of logistics in manufacturing?
Logistics are an essential component of any business. They are essential to any business's success.
Logistics also play a major role in reducing costs and increasing efficiency.
Is automation important in manufacturing?
Automation is essential for both manufacturers and service providers. Automation allows them to deliver services quicker and more efficiently. In addition, it helps them reduce costs by reducing human errors and improving productivity.
What is the job of a logistics manger?
Logistics managers ensure that goods arrive on time and are unharmed. This is achieved by using their knowledge and experience with the products of the company. He/she should make sure that enough stock is on hand to meet the demands.
What are the differences between these four types?
Manufacturing refers the process of turning raw materials into useful products with machines and processes. It includes many different activities like designing, building and testing, packaging, shipping and selling, as well as servicing.
What is production planning?
Production planning is the process of creating a plan that covers all aspects of production. This includes scheduling, budgeting and crew, location, equipment, props, and more. It is important to have everything ready and planned before you start shooting. This document should include information about how to achieve the best results on-set. This information includes locations, crew details and equipment requirements.
First, you need to plan what you want to film. You may already know where you want the film to be shot, or perhaps you have specific locations and sets you wish to use. Once you have identified the scenes and locations, you can start to determine which elements are required for each scene. Perhaps you have decided that you need to buy a car but aren't sure which model. If this is the case, you might start searching online for car models and then narrow your options by selecting from different makes.
Once you have found the right car, you can start thinking about extras. What about additional seating? Maybe you need someone to move around in the back. Maybe you'd like to change the interior from black to a white color. These questions will help you determine the exact look and feel of your car. Also, think about what kind of shots you would like to capture. Will you be filming close-ups or wide angles? Maybe you want to show your engine or the steering wheel. These factors will help you determine which car style you want to film.
Once you have all the information, you are ready to create a plan. A schedule will tell you when you need to start shooting and when you need to finish. Every day will have a time for you to arrive at the location, leave when you are leaving and return home when you are done. Everyone will know what they need and when. You can also make sure to book extra staff in advance if you have to hire them. It's not worth paying someone to show up if you haven't told him.
Also, consider how many days you will be filming your schedule. Some projects are quick and easy, while others take weeks. While creating your schedule, it is important to remember whether you will require more than one shot per day. Multiple takes at the same place will result in higher costs and longer completion times. It is better to be cautious and take fewer shots than you risk losing money if you are not sure if multiple takes are necessary.
Budget setting is an important part of production planning. You will be able to manage your resources if you have a realistic budget. Remember that you can always reduce the budget later on if you run into unforeseen problems. However, you shouldn't overestimate the amount of money you will spend. You'll end up with less money after paying for other things if the cost is underestimated.
Production planning is a very detailed process, but once you understand how everything works together, it becomes easier to plan future projects.
Statistics
- In the United States, for example, manufacturing makes up 15% of the economic output. (twi-global.com)
- (2:04) MTO is a production technique wherein products are customized according to customer specifications, and production only starts after an order is received. (oracle.com)
- According to the United Nations Industrial Development Organization (UNIDO), China is the top manufacturer worldwide by 2019 output, producing 28.7% of the total global manufacturing output, followed by the United States, Japan, Germany, and India.[52][53] (en.wikipedia.org)
- According to a Statista study, U.S. businesses spent $1.63 trillion on logistics in 2019, moving goods from origin to end user through various supply chain network segments. (netsuite.com)
- In 2021, an estimated 12.1 million Americans work in the manufacturing sector.6 (investopedia.com)
External Links
How To
How to use the Just-In Time Method in Production
Just-in time (JIT), is a process that reduces costs and increases efficiency in business operations. It's a way to ensure that you get the right resources at just the right time. This means that only what you use is charged to your account. The term was first coined by Frederick Taylor, who developed his theory while working as a foreman in the early 1900s. He saw how overtime was paid to workers for work that was delayed. He concluded that if workers were given enough time before they start work, productivity would increase.
The idea behind JIT is that you should plan ahead and have everything ready so you don't waste money. It is important to look at your entire project from beginning to end and ensure that you have enough resources to handle any issues that may arise. If you expect problems to arise, you will be able to provide the necessary equipment and personnel to address them. You won't have to pay more for unnecessary items.
There are several types of JIT techniques:
-
Demand-driven JIT: This is a JIT that allows you to regularly order the parts/materials necessary for your project. This will enable you to keep track of how much material is left after you use it. You'll also be able to estimate how long it will take to produce more.
-
Inventory-based: This allows you to store the materials necessary for your projects in advance. This allows for you to anticipate how much you can sell.
-
Project-driven: This approach involves setting aside sufficient funds to cover your project's costs. Knowing how much money you have available will help you purchase the correct amount of materials.
-
Resource-based: This is the most common form of JIT. Here, you allocate certain resources based on demand. If you have many orders, you will assign more people to manage them. If there aren't many orders, you will assign fewer people.
-
Cost-based: This is a similar approach to resource-based but you are not only concerned with how many people you have, but also how much each one costs.
-
Price-based: This approach is very similar to the cost-based method except that you don't look at individual workers costs but the total cost of the company.
-
Material-based: This is very similar to cost-based but instead of looking at total costs of the company you are concerned with how many raw materials you use on an average.
-
Time-based JIT is another form of resource-based JIT. Instead of focusing on the cost of each employee, you will focus on the time it takes to complete a project.
-
Quality-based JIT: Another variation on resource-based JIT. Instead of worrying about the costs of each employee or how long it takes for something to be made, you should think about how quality your product is.
-
Value-based JIT: This is the latest form of JIT. In this case, you're not concerned with how well the products perform or whether they meet customer expectations. Instead, you focus on the added value that you provide to your market.
-
Stock-based: This is an inventory-based method that focuses on the actual number of items being produced at any given time. This method is useful when you want to increase production while decreasing inventory.
-
Just-in time (JIT), planning: This is a combination JIT/supply chain management. It refers to the process of scheduling the delivery of components as soon as they are ordered. This is important as it reduces lead time and increases throughput.