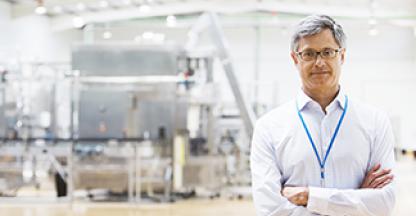
Depending on the employer, the duties of a mechanical engineering technician will vary. They will test equipment, review blueprints and write purchase orders. They could also be exposed to potentially dangerous materials. However, with proper procedures, these risks are minimal.
A mechanical engineer supervises the duties of a technician in mechanical engineering. However, they can also work independently. They are responsible for the maintenance and repair of machinery and equipment. They are responsible for ensuring safety and compliance with company policies. Customers' requirements must also be met.
A good mechanical engineering technician will be able to solve mechanical problems and make accurate calculations. They may also work closely alongside engineers to improve production processes. They may also be able to design new equipment or test new materials.
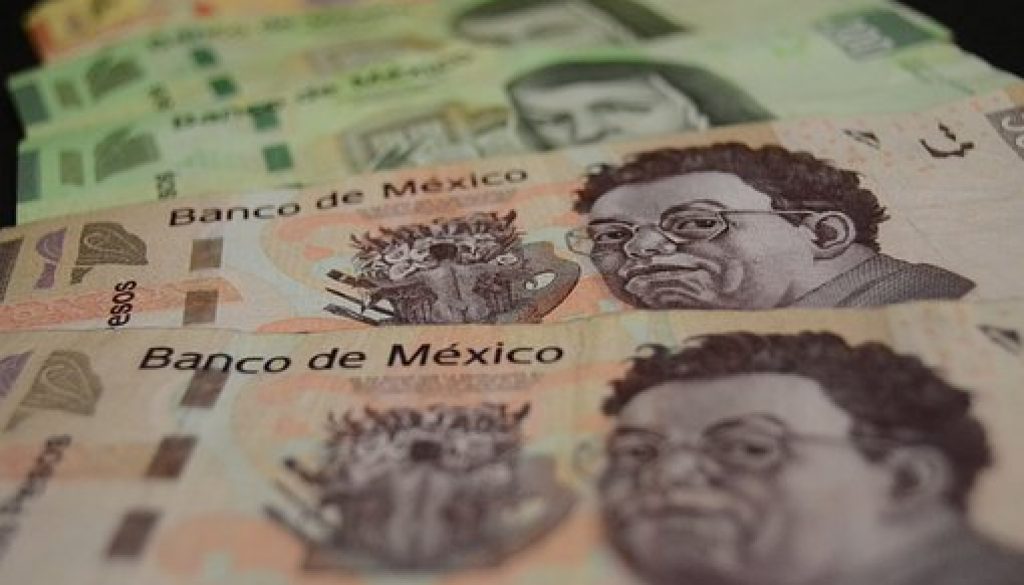
To get the best job, a mechanical engineering technician must have a solid knowledge of mechanical engineering principles and practices. To design and analyze mechanical systems, they should be proficient with CAD software. They will also need to be able to maintain mechanical service records. They should also be able manage time well.
Mechanical engineers technicians are most commonly responsible for testing equipment and making estimations. They may also do research to improve manufacturing processes. These findings are typically recorded and evaluated making them an important part a technician in mechanical engineering.
Mechanical engineers also have other duties, such as writing work orders, translating instructions, estimating labor costs, and creating sketches for parts. To test the functionality of electrical equipment and systems, mechanical engineers can also test them. They may also be involved in the design of industrial machinery, power plants, or other related systems. They can also conduct statistical analyses to determine the production costs.
To become a successful mechanic technician you must have a solid understanding of mechanical engineering principles, critical thinking skills and an eye for detail. Knowledge of new technology is also a requirement. Engineers will require you to draw and test mechanical systems under different operating conditions.
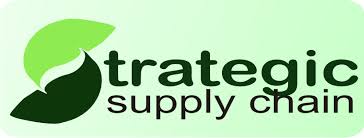
Another important component of a mechanical engineering technician's job is the quality control analysis. In this process, engineers evaluate the performance of tool drawings by comparing the designs to the original specifications. They may also make improvements and record the results. They may also submit the results to engineering.
A mechanical engineer technician can work long hours, but will be expected to work regular hours. Sometimes, they may work overtime. They may work in a lab, research facility, or manufacturing plant. They may work a variety of hours and be exposed to potentially hazardous materials.
The mechanical engineering technician might also need to be familiar with hydraulics and other power systems. They will need to use power tools on a daily base and rigging equipment in order to meet the needs their customers.
FAQ
What do you mean by warehouse?
Warehouses and storage facilities are where goods are kept before being sold. It can be an outdoor or indoor area. In some cases, it may be a combination of both.
What are the 7 Rs of logistics?
The acronym 7R's for Logistics stands to represent the seven basic principles in logistics management. It was developed by International Association of Business Logisticians (IABL), and published as part of their "Seven Principles of Logistics Management Series" in 2004.
The acronym is made up of the following letters:
-
Responsible – ensure that all actions are legal and don't cause harm to anyone else.
-
Reliable - Have confidence in your ability to fulfill all of your commitments.
-
Reasonable - use resources efficiently and don't waste them.
-
Realistic - Consider all aspects of operations, including environmental impact and cost effectiveness.
-
Respectful - treat people fairly and equitably.
-
Resourceful - look for opportunities to save money and increase productivity.
-
Recognizable provides value-added products and services to customers
What is production management?
Production planning is the process of creating a plan that covers all aspects of production. This includes scheduling, budgeting and crew, location, equipment, props, and more. It is important to have everything ready and planned before you start shooting. This document should include information about how to achieve the best results on-set. This includes information on shooting times, locations, cast lists and crew details.
The first step is to decide what you want. You may have decided where to shoot or even specific locations you want to use. Once you have identified your locations and scenes, you can start working out which elements you require for each scene. You might decide you need a car, but not sure what make or model. You could look online for cars to see what options are available, and then narrow down your choices by selecting between different makes or models.
After you have selected the car you want, you can begin to think about additional features. Are you looking for people to sit in the front seats? Or maybe you just need someone to push the car around. Maybe you'd like to change the interior from black to a white color. These questions will help to determine the style and feel of your car. Another thing you can do is think about what type of shots are desired. Will you be filming close-ups or wide angles? Maybe you want to show the engine and the steering wheel. This will allow you to determine the type of car you want.
Once you have established all the details, you can create a schedule. The schedule will show you when to begin shooting and when to stop. The schedule will show you when to get there, what time to leave, and when to return home. This way, everyone knows what they need to do and when. Book extra staff ahead of time if you need them. It's not worth paying someone to show up if you haven't told him.
Your schedule will also have to be adjusted to reflect the number of days required to film. Some projects may only take a couple of days, while others could last for weeks. You should consider whether you will need more than one shot per week when creating your schedule. Multiple shots at the same location can increase costs and make it more difficult to complete. It's better to be safe than sorry and shoot less takes if you're not certain whether you need more takes.
Budget setting is another important aspect in production planning. As it will allow you and your team to work within your financial means, setting a realistic budget is crucial. You can always lower the budget if you encounter unexpected problems. However, you shouldn't overestimate the amount of money you will spend. Underestimating the cost will result in less money after you have paid for other items.
Production planning is a very detailed process, but once you understand how everything works together, it becomes easier to plan future projects.
How important is automation in manufacturing?
Not only is automation important for manufacturers, but it's also vital for service providers. Automation allows them to deliver services quicker and more efficiently. It reduces human errors and improves productivity, which in turn helps them lower their costs.
What are the jobs in logistics?
There are different kinds of jobs available in logistics. Here are some examples:
-
Warehouse workers – They load, unload and transport pallets and trucks.
-
Transportation drivers: They drive trucks and trailers and deliver goods and make pick-ups.
-
Freight handlers: They sort and package freight in warehouses.
-
Inventory managers – They manage the inventory in warehouses.
-
Sales representatives - They sell products.
-
Logistics coordinators are responsible for organizing and planning logistics operations.
-
Purchasing agents are those who purchase goods and services for the company.
-
Customer service agents - They answer phone calls and respond to emails.
-
Shipping clerks - They process shipping orders and issue bills.
-
Order fillers are people who fill orders based only on what was ordered.
-
Quality control inspectors (QCI) - They inspect all incoming and departing products for potential defects.
-
Others - There is a variety of other jobs in logistics. These include transportation supervisors and cargo specialists.
Statistics
- According to a Statista study, U.S. businesses spent $1.63 trillion on logistics in 2019, moving goods from origin to end user through various supply chain network segments. (netsuite.com)
- According to the United Nations Industrial Development Organization (UNIDO), China is the top manufacturer worldwide by 2019 output, producing 28.7% of the total global manufacturing output, followed by the United States, Japan, Germany, and India.[52][53] (en.wikipedia.org)
- (2:04) MTO is a production technique wherein products are customized according to customer specifications, and production only starts after an order is received. (oracle.com)
- It's estimated that 10.8% of the U.S. GDP in 2020 was contributed to manufacturing. (investopedia.com)
- In 2021, an estimated 12.1 million Americans work in the manufacturing sector.6 (investopedia.com)
External Links
How To
How to use the Just In-Time Production Method
Just-in-time (JIT) is a method that is used to reduce costs and maximize efficiency in business processes. It is a process where you get the right amount of resources at the right moment when they are needed. This means that you only pay the amount you actually use. Frederick Taylor, a 1900s foreman, first coined the term. After observing how workers were paid overtime for late work, he realized that overtime was a common practice. He concluded that if workers were given enough time before they start work, productivity would increase.
JIT is an acronym that means you need to plan ahead so you don’t waste your money. Look at your entire project, from start to end. Make sure you have enough resources in place to deal with any unexpected problems. If you expect problems to arise, you will be able to provide the necessary equipment and personnel to address them. This will ensure that you don't spend more money on things that aren't necessary.
There are several types of JIT techniques:
-
Demand-driven: This JIT is where you place regular orders for the parts/materials that are needed for your project. This will allow for you to track the material that you have left after using it. This will allow to you estimate the time it will take for more to be produced.
-
Inventory-based: This type allows you to stock the materials needed for your projects ahead of time. This allows one to predict how much they will sell.
-
Project-driven: This is an approach where you set aside enough funds to cover the cost of your project. If you know the amount you require, you can buy the materials you need.
-
Resource-based JIT: This is the most popular form of JIT. Here, you allocate certain resources based on demand. You might assign more people to help with orders if there are many. If you don't have many orders, you'll assign fewer people to handle the workload.
-
Cost-based: This is similar to resource-based, except that here you're not just concerned about how many people you have but how much each person costs.
-
Price-based pricing: This is similar in concept to cost-based but instead you look at how much each worker costs, it looks at the overall company's price.
-
Material-based: This is very similar to cost-based but instead of looking at total costs of the company you are concerned with how many raw materials you use on an average.
-
Time-based: This is another variation of resource-based JIT. Instead of worrying about how much each worker costs, you can focus on how long the project takes.
-
Quality-based JIT: Another variation on resource-based JIT. Instead of looking at the labor costs and time it takes to make a product, think about its quality.
-
Value-based JIT: One of the most recent forms of JIT. In this scenario, you're not concerned about how products perform or whether customers expect them to meet their expectations. Instead, you focus on the added value that you provide to your market.
-
Stock-based: This stock-based method focuses on the actual quantity of products being made at any given time. It's useful when you want maximum production and minimal inventory.
-
Just-in time (JIT), planning: This is a combination JIT/supply chain management. It's the process of scheduling delivery of components immediately after they are ordered. It's important as it reduces leadtimes and increases throughput.