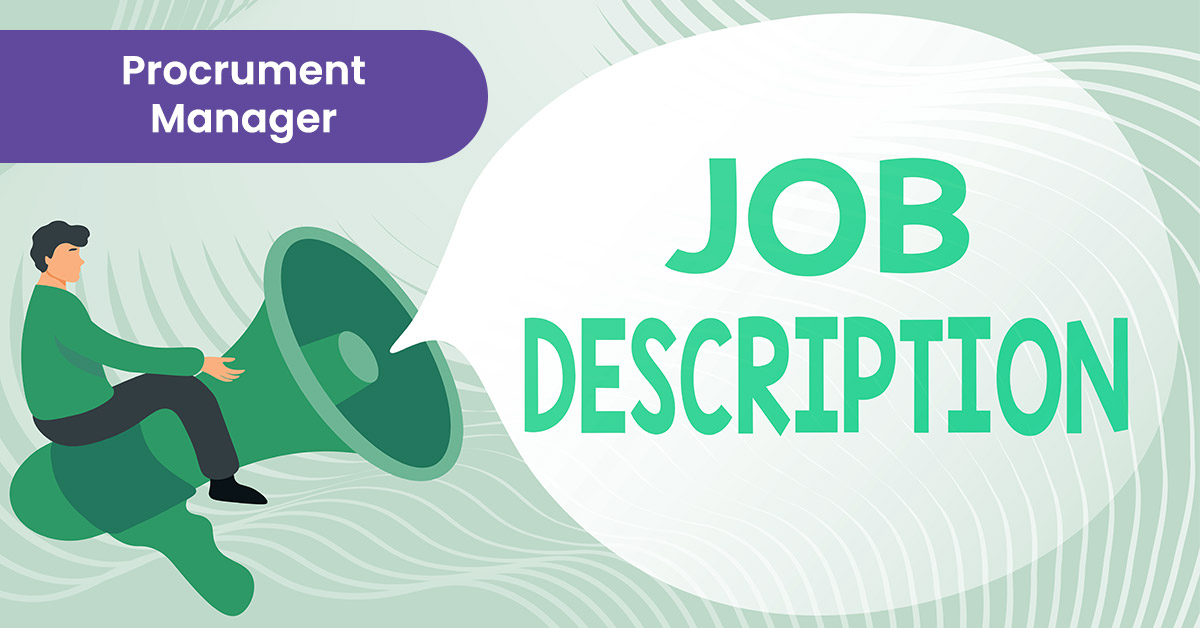
Six-Sigma, lean and Lean are complementary methods of improving processes. Although they both have the same tools for problem solving, each has its strengths and weaknesses. Six-Sigma refers to a statistical control technique. Lean, on the other hand, starts with the assumption that a product should add value to its customers, not just make it. Lean means reducing waste and increasing the quality of the product being made.
Problem solving in PDCA
There are some differences between PDCA and DMAIC problem solving, but both are based on the DMAIC approach. The PDCA cycle requires more planning and analysis. PDCA isn't as efficient for solving urgent issues like DMAIC. This approach requires a problem solver with technical skills. Six Sigma will require a problem-solving team lead who is a Six Sigma "green belt" certified practitioner.
Six Sigma follows a cycle first introduced by W. Edwards Deming back in 1950s. It was designed to be used with continuous improvement methods in order to rebuild Japan's industry. The P (Plan) stage requires real data to be gathered and a clear mission. After the PDCA phase, the team must agree on a solution.
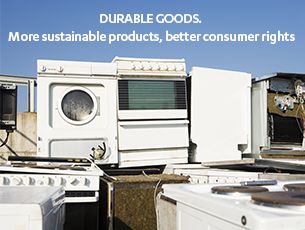
Process maps
There is one key difference between Six Sigma process maps and Lean. It's how each method describes the processes. Both emphasize defining a process in detail, but each methodology focuses on different aspects of the process. Lean, for example, focuses on mapping actual processes and not standard operating procedures. When creating process diagrams, you should consider the major decisions, activities, and sources for approval. Consider areas that use multiple methods, factors, and other obstacles. Make sure you match the roles and look at the process flow.
A process map should include steps, symbols, and arrows to show the flow of a process. To ensure that each process accurately depicts the actual process, several people should review it. Also, a process map should include the date it was created and who to contact if there are any questions. Overall process maps can help improve a process. They can be too complex.
Analysis of cause and effect
Six Sigma and lean project management techniques include statistical analysis and stochastic optimizing. The Cause and Effect Matrix is a way to link the steps in a process with their outputs and inputs. The customer's requirements will be listed in the order that they are most important. Inputs, outputs, and their impact on the outcome are ranked. Key process input variables and their ranking should be determined.
While each technique has a unique set of benefits, they are not the same. Lean Six Sigma utilizes a process-improvement methodology that is based in Frederick Winslow Taylor’s Principles of Scientific Management. Taylor understood business processes as interconnected processes that are linked together. He also recommended reducing variation. Six-Sigma (and lean) are complementary in the effort to reduce waste.
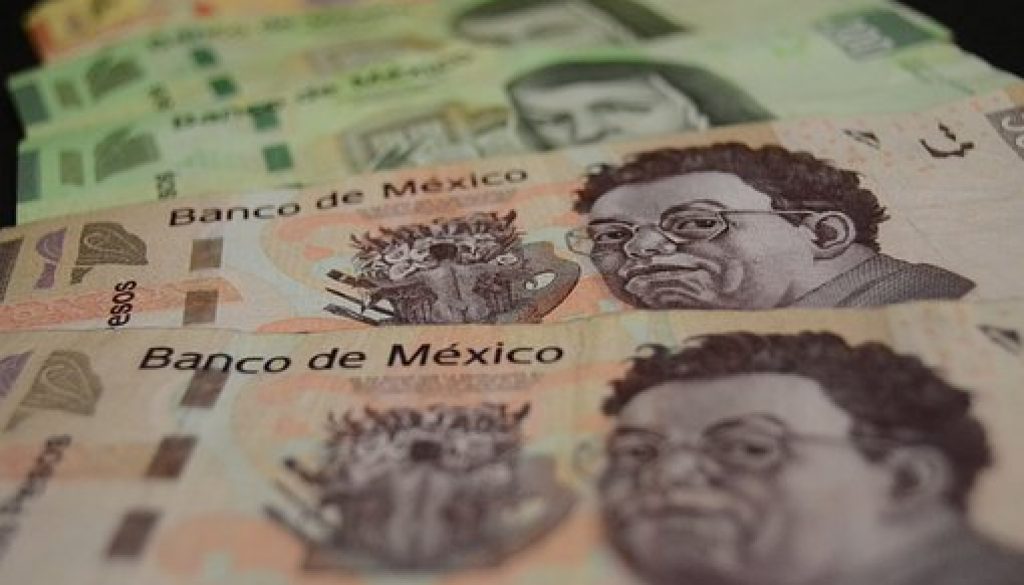
Eliminating variation
Variation is a natural part of any manufacturing process. Variability in manufacturing processes can cause uncertainty regarding the outcome. To provide professional results, consistency is necessary. Predictable output is achieved by eliminating variation in Six Sigma and Lean manufacturing processes. Variation is OK. However, too much variation can lead the to repairs, rework, as well as possible out-of-business consequences. The best way to manage variation is to identify the root cause.
The first place to look for variations is at decision points. Process maps identify decision points, which are represented by diamonds. Six Sigma teams can begin by identifying decision points, and then start eliminating variations. The information is obtained from the process owner or the Six Sigma team. The Six Sigma team will not be able to focus if the process owner does not follow a standard procedure. A process map might not work if the Six Sigma team lacks the technical capability to make necessary adjustments.
FAQ
What are the 7 Rs of logistics?
The acronym "7R's" of Logistics stands for seven principles that underpin logistics management. It was developed by the International Association of Business Logisticians (IABL) and published in 2004 as part of its "Seven Principles of Logistics Management" series.
The following letters form the acronym:
-
Responsible - to ensure that all actions are within the legal requirements and are not detrimental to others.
-
Reliable - have confidence in the ability to deliver on commitments made.
-
Reasonable - use resources efficiently and don't waste them.
-
Realistic – Consider all aspects, including cost-effectiveness as well as environmental impact.
-
Respectful – Treat others fairly and equitably.
-
Reliable - Find ways to save money and increase your productivity.
-
Recognizable is a company that provides customers with value-added solutions.
What are the products of logistics?
Logistics involves the transportation of goods from point A and point B.
They include all aspects of transport, including packaging, loading, transporting, unloading, storing, warehousing, inventory management, customer service, distribution, returns, and recycling.
Logisticians ensure that the product is delivered to the correct place, at the right time, and under safe conditions. They assist companies with their supply chain efficiency through information on demand forecasts. Stock levels, production times, and availability.
They also keep track of shipments in transit, monitor quality standards, perform inventories and order replenishment, coordinate with suppliers and vendors, and provide support services for sales and marketing.
How does a Production Planner differ from a Project Manager?
The difference between a product planner and project manager is that a planer is typically the one who organizes and plans the entire project. A production planner, however, is mostly involved in the planning stages.
Statistics
- You can multiply the result by 100 to get the total percent of monthly overhead. (investopedia.com)
- Many factories witnessed a 30% increase in output due to the shift to electric motors. (en.wikipedia.org)
- In the United States, for example, manufacturing makes up 15% of the economic output. (twi-global.com)
- It's estimated that 10.8% of the U.S. GDP in 2020 was contributed to manufacturing. (investopedia.com)
- (2:04) MTO is a production technique wherein products are customized according to customer specifications, and production only starts after an order is received. (oracle.com)
External Links
How To
How to Use Just-In-Time Production
Just-in-time (JIT) is a method that is used to reduce costs and maximize efficiency in business processes. It is a process where you get the right amount of resources at the right moment when they are needed. This means that your only pay for the resources you actually use. Frederick Taylor first coined this term while working in the early 1900s as a foreman. After observing how workers were paid overtime for late work, he realized that overtime was a common practice. He concluded that if workers were given enough time before they start work, productivity would increase.
JIT teaches you to plan ahead and prepare everything so you don’t waste time. You should also look at the entire project from start to finish and make sure that you have sufficient resources available to deal with any problems that arise during the course of your project. You will have the resources and people to solve any problems you anticipate. This way, you won't end up paying extra money for things that weren't really necessary.
There are many JIT methods.
-
Demand-driven: This is a type of JIT where you order the parts/materials needed for your project regularly. This will let you track the amount of material left over after you've used it. This will allow you to calculate how long it will take to make more.
-
Inventory-based: You stock materials in advance to make your projects easier. This allows one to predict how much they will sell.
-
Project-driven: This means that you have enough money to pay for your project. If you know the amount you require, you can buy the materials you need.
-
Resource-based JIT is the most widespread form. Here you can allocate certain resources based purely on demand. You will, for example, assign more staff to deal with large orders. If you don’t have many orders you will assign less people to the work.
-
Cost-based: This approach is very similar to resource-based. However, you don't just care about the number of people you have; you also need to consider how much each person will cost.
-
Price-based: This is very similar to cost-based, except that instead of looking at how much each individual worker costs, you look at the overall price of the company.
-
Material-based: This is very similar to cost-based but instead of looking at total costs of the company you are concerned with how many raw materials you use on an average.
-
Time-based: This is another variation of resource-based JIT. Instead of focusing on the cost of each employee, you will focus on the time it takes to complete a project.
-
Quality-based: This is yet another variation of resource-based JIT. Instead of looking at the labor costs and time it takes to make a product, think about its quality.
-
Value-based JIT is the newest form of JIT. In this scenario, you're not concerned about how products perform or whether customers expect them to meet their expectations. Instead, your goal is to add value to the market.
-
Stock-based. This method is inventory-based and focuses only on the actual production at any given point. This method is useful when you want to increase production while decreasing inventory.
-
Just-in-time (JIT) planning: This is a combination of JIT and supply chain management. It's the process of scheduling delivery of components immediately after they are ordered. It reduces lead times and improves throughput.