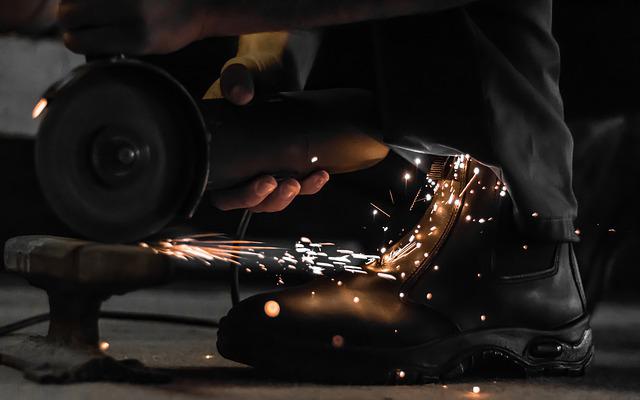
An industrial manager is an engineer who integrates different engineering processes to create an efficient management system. These engineering processes are integrated into an integrated management system by the industrial manager. Here are some things you should know about the job. Below are some requirements and benefits for industrial managers. If you have the required qualifications and are looking for a challenging and rewarding job, this is the career for you. Continue reading to find out more.
Job description
An industrial manager oversees the processes involved in the manufacturing and production of goods and services. This job will cover many aspects of production, but it will also include how to source raw materials or implement equipment. Computer literacy is essential for industrial production managers, who must be able to use computers to coordinate the work of different departments, suppliers, clients, and other parties. Industrial production managers should be knowledgeable about the latest management techniques and production technologies. Many managers take part in professional organizations, attend tradeshows and conferences in the industry, and enroll in courses to earn certification.
Industrial managers coordinate various departments within a company and oversee manufacturing processes. They make sure production lines run smoothly and meet customers' time and quality requirements. They also oversee the staffing levels and make changes to production levels if necessary to reduce inventory. They may coordinate communication with suppliers or other departments, and supervise quality control programs. A majority of this role involves managing people, which includes identifying, training, and motivating employees.
Education is required
Obtaining a bachelor's degree in business administration, management, or engineering is not typically enough to qualify as an industrial manager. Some employers prefer candidates with a background or education in these areas. Also, industrial managers must be computer-literate. Computers are becoming increasingly essential in the manufacturing process. They help coordinate production between departments, suppliers, clients, and other parties. In order to succeed in this field, individuals interested should have the appropriate education and experience.
Many industrial production managers started their careers as production workers before moving up to the first-line supervisory position. A college degree in business administration is required to advance to an industrial management position. However, some entry-level workers may be able to gain this education on the job, or they may choose to take classes sponsored by their companies. However, managers must have two to five year of relevant experience before becoming a manager.
Potential earnings

Industrial managers work in manufacturing plants and oversee the smooth operation of the entire process. They are responsible for determining how best to utilize equipment and employees, as well as making strategic decisions. Their responsibilities include hiring, evaluating, and setting production times, and making sure safety procedures are adhered to. They also oversee the day-to-day activities of a team of workers and continuously analyze the entire production process to ensure it is operating efficiently and at peak efficiency.
The earnings potential of an industrial production manager depends on the employer and the experience of the employee. While it's difficult to predict the future earnings of industrial managers, the average salary in May 2016 was $103,380, with the highest paid industrial production managers earning $172,150 annually. Also, higher earnings are possible for industrial production managers who have had advanced training and certification. According to the U.S. Bureau of Labor Statistics industrial production managers who have earned a bachelor’s degree or higher could earn more.
Work environment
A manager of industrial production divides their time between the production floor or an office. Sometimes, they live in the same building. Industrial production managers must observe established health and safety practices and wear appropriate protective equipment when working in a production area. They also spend significant amounts of time in meetings with subordinates and analyzing production data. These managers might also create reports. An industrial production manager's work environment can be dynamic.
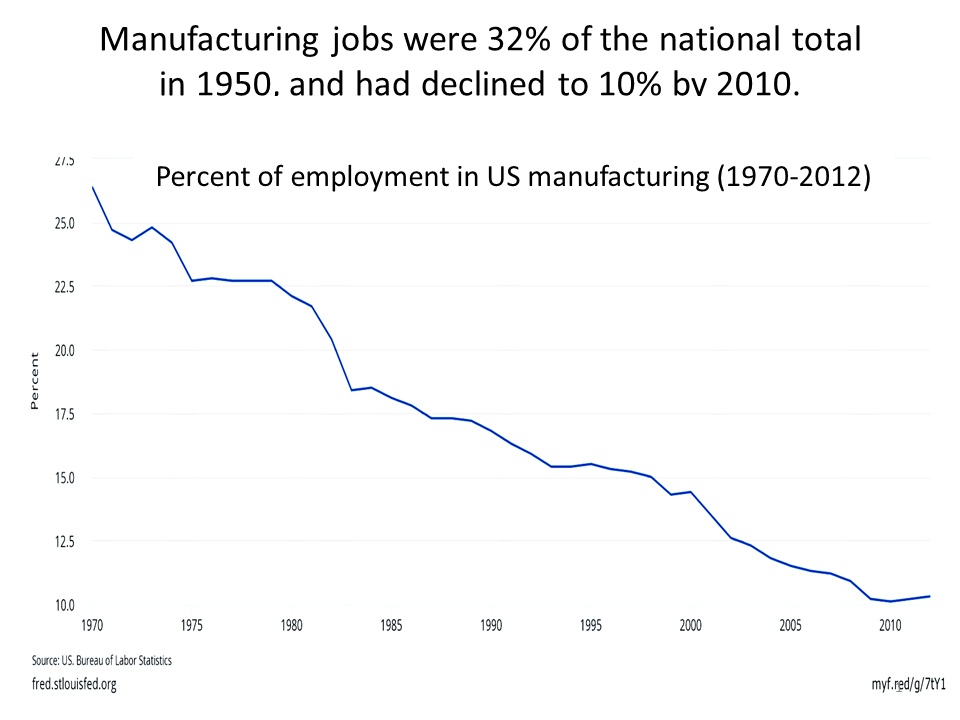
Industrial production managers are an integral part of the business's management structure. They have many responsibilities. They are responsible for coordinating the activities of workers and increasing productivity. Increasing productivity and ensuring safety are some of the primary responsibilities of an industrial production manager. Corporate restructuring has resulted in many levels of managerial and support staff being eliminated. Production managers now have a greater workload. This can present a serious challenge to any manager and make the job of a producer manager more difficult.
FAQ
What are the 7 Rs of logistics management?
The acronym 7R's of Logistic is an acronym that stands for seven fundamental principles of logistics management. It was developed and published by the International Association of Business Logisticians in 2004 as part of the "Seven Principles of Logistics Management".
The following letters make up the acronym:
-
Responsible - to ensure that all actions are within the legal requirements and are not detrimental to others.
-
Reliable - You can have confidence that you will fulfill your promises.
-
It is reasonable to use resources efficiently and not waste them.
-
Realistic - consider all aspects of operations, including cost-effectiveness and environmental impact.
-
Respectful: Treat others with fairness and equity
-
Reliable - Find ways to save money and increase your productivity.
-
Recognizable provides value-added products and services to customers
What are the requirements to start a logistics business?
To run a successful logistics company, you need a lot knowledge and skills. Good communication skills are essential to effectively communicate with your suppliers and clients. You need to understand how to analyze data and draw conclusions from it. You must be able manage stress and pressure under pressure. You need to be innovative and creative to come up with new ways to increase efficiency. You need to have strong leadership qualities to motivate team members and direct them towards achieving organizational goals.
You should also be organized and efficient to meet tight deadlines.
What are the goods of logistics?
Logistics refers to all activities that involve moving goods from A to B.
These include all aspects related to transport such as packaging, loading and transporting, storing, transporting, unloading and warehousing inventory management, customer service. Distribution, returns, recycling are some of the options.
Logisticians make sure that the right product arrives at the right place at the correct time and in safe conditions. They provide information on demand forecasts as well stock levels, production schedules and availability of raw material.
They also keep track of shipments in transit, monitor quality standards, perform inventories and order replenishment, coordinate with suppliers and vendors, and provide support services for sales and marketing.
What are the responsibilities for a manufacturing manager
The manufacturing manager should ensure that every manufacturing process is efficient and effective. They should also be aware and responsive to any company problems.
They should also be able and comfortable communicating with other departments like sales and marketing.
They should also be knowledgeable about the latest trends in the industry so they can use this information for productivity and efficiency improvements.
What is meant by manufacturing industries?
Manufacturing Industries is a group of businesses that produce goods for sale. These products are sold to consumers. This is accomplished by using a variety of processes, including production, distribution and retailing. They manufacture goods from raw materials using machines and other equipment. This includes all types manufactured goods such as clothing, building materials, furniture, electronics, tools and machinery.
How does manufacturing avoid bottlenecks in production?
To avoid production bottlenecks, ensure that all processes run smoothly from the moment you receive your order to the time the product ships.
This includes both quality control and capacity planning.
Continuous improvement techniques such Six Sigma can help you achieve this.
Six Sigma Management System is a method to increase quality and reduce waste throughout your organization.
It seeks to eliminate variation and create consistency in your work.
What are manufacturing and logistic?
Manufacturing refers to the process of making goods using raw materials and machines. Logistics covers all aspects involved in managing supply chains, including procurement and production planning. Manufacturing and logistics are often considered together as a broader term that encompasses both the process of creating products and delivering them to customers.
Statistics
- [54][55] These are the top 50 countries by the total value of manufacturing output in US dollars for its noted year according to World Bank.[56] (en.wikipedia.org)
- According to the United Nations Industrial Development Organization (UNIDO), China is the top manufacturer worldwide by 2019 output, producing 28.7% of the total global manufacturing output, followed by the United States, Japan, Germany, and India.[52][53] (en.wikipedia.org)
- In the United States, for example, manufacturing makes up 15% of the economic output. (twi-global.com)
- Job #1 is delivering the ordered product according to specifications: color, size, brand, and quantity. (netsuite.com)
- It's estimated that 10.8% of the U.S. GDP in 2020 was contributed to manufacturing. (investopedia.com)
External Links
How To
How to use 5S in Manufacturing to Increase Productivity
5S stands for "Sort", "Set In Order", "Standardize", "Separate" and "Store". Toyota Motor Corporation developed the 5S method in 1954. It assists companies in improving their work environments and achieving higher efficiency.
The basic idea behind this method is to standardize production processes, so they become repeatable, measurable, and predictable. This means that every day tasks such cleaning, sorting/storing, packing, and labeling can be performed. Because workers know what they can expect, this helps them perform their jobs more efficiently.
Five steps are required to implement 5S: Sort, Set In Order, Standardize. Separate. Each step requires a different action to increase efficiency. Sorting things makes it easier to find them later. When you set items in an order, you put items together. You then organize your inventory in groups. Labeling your containers will ensure that everything is correctly labeled.
This process requires employees to think critically about how they do their job. Employees need to understand the reasons they do certain jobs and determine if there is a better way. They must learn new skills and techniques in order to implement the 5S system.
The 5S Method not only improves efficiency, but it also helps employees to be more productive and happier. They will feel motivated to strive for higher levels of efficiency once they start to see results.